+8613776545860
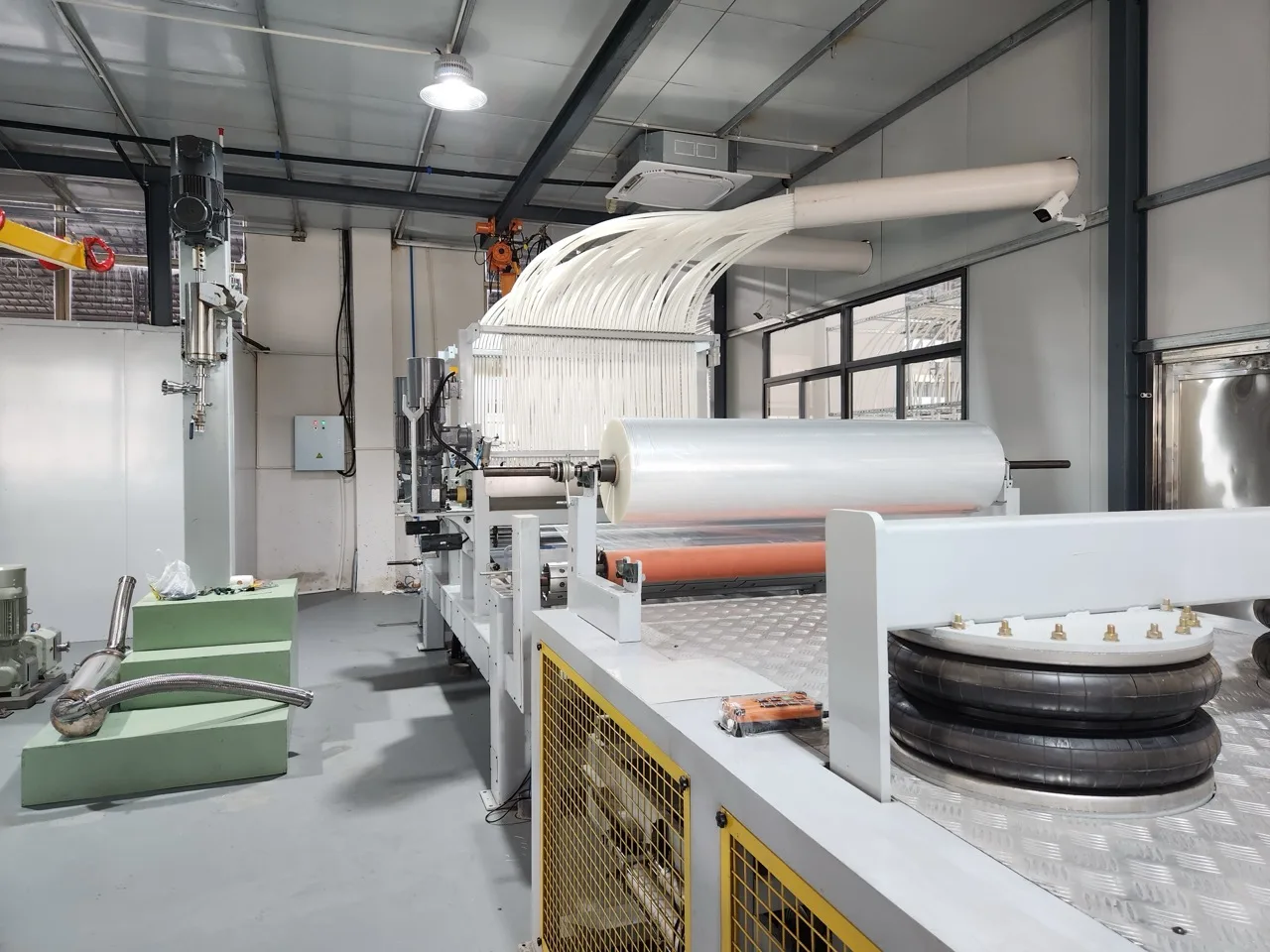
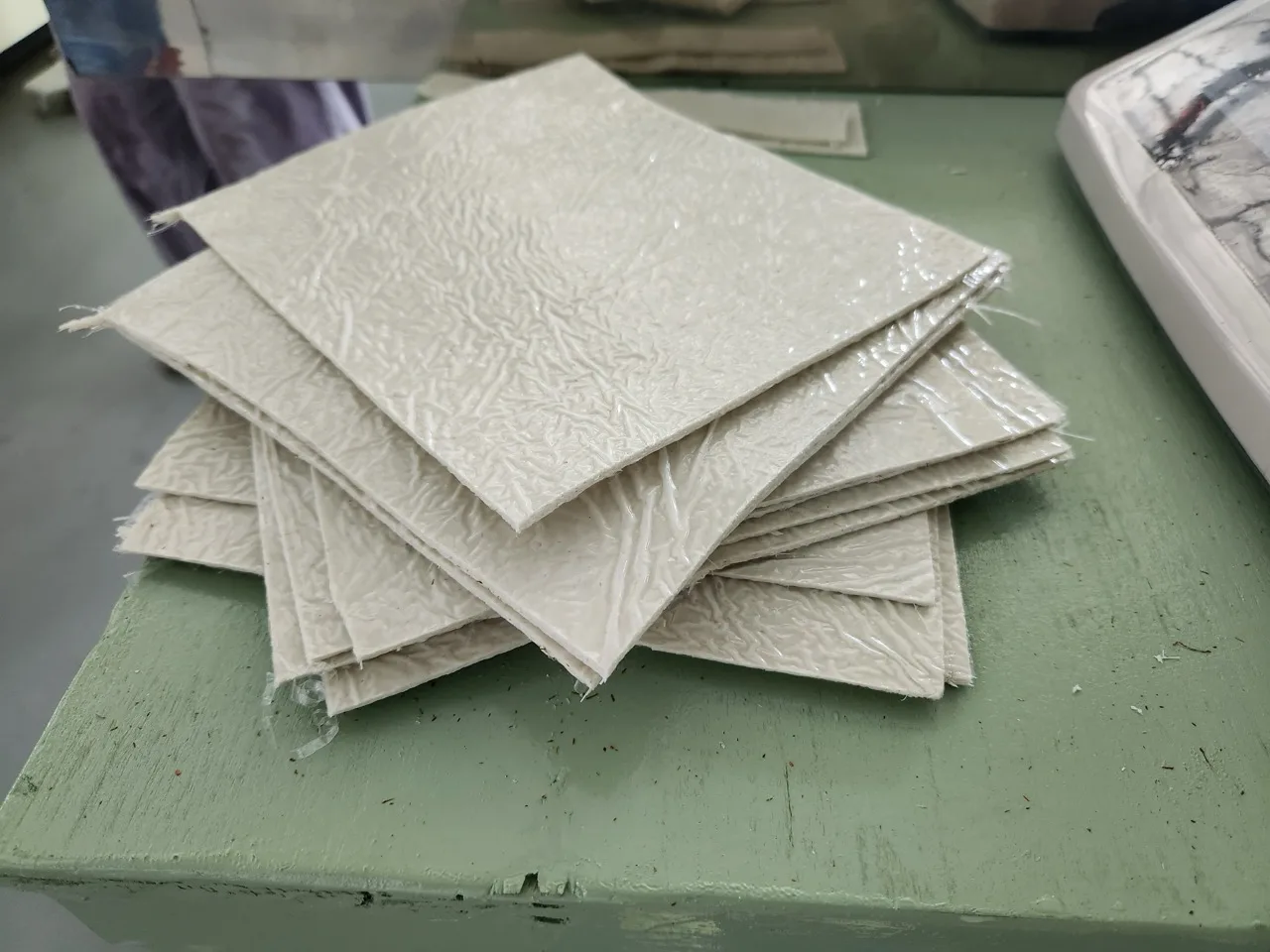
What is Sheet Molding Compound (SMC)?
SMC is a composite material made of glass fibers, fillers, and resins, blended into a sheet form. This material is molded into complex shapes, making it suitable for mass production of lightweight, durable parts. The composition typically includes unsaturated polyester or vinyl ester resin, giving SMC its robust mechanical and chemical properties. Due to its composition, SMC can withstand harsh environmental conditions, chemical exposure, and heavy loads, making it ideal for a wide range of applications.
Key Advantages of SMC
1. High Strength and Durability
SMC offers impressive strength-to-weight ratios, comparable to some metals. The addition of glass fibers in SMC enhances its structural integrity, allowing for high durability without the added weight.
2. Excellent Electrical Insulation
SMC is inherently insulating, which makes it an excellent material for electrical applications. Its resistance to electrical conductivity and thermal stability makes it popular in electrical enclosures and components.
3. Cost-Effective Mass Production
The production process of SMC allows for the efficient manufacturing of complex shapes in large volumes. Unlike metals, SMC can be molded into detailed parts without extensive machining, making it a cost-effective alternative for high-quantity production.
4. Corrosion Resistance
The thermoset resin matrix in SMC provides excellent resistance to corrosion, making it suitable for applications where parts are exposed to moisture, chemicals, or extreme temperatures.
5. Lightweight and Environmentally Friendly
Compared to metals like steel or aluminum, SMC is lighter, reducing the overall weight of products. This can lead to significant energy savings, particularly in the automotive and transportation industries.
Common Applications of SMC
1. Automotive Industry
Automotive manufacturers use SMC for producing body panels, bumpers, and hoods, taking advantage of its lightweight, corrosion-resistant, and impact-resistant qualities. SMC is also used in electric vehicles for battery enclosures and underbody shields, where insulation and lightweight design are critical.
2. Electrical and Electronics Industry
Due to its non-conductive nature, SMC is widely used in electrical enclosures, transformer housings, and circuit breaker parts. Its ability to insulate and resist heat is crucial for ensuring safety and performance in high-voltage environments.
3. Construction and Infrastructure
The construction industry benefits from SMC’s durability and resistance to environmental degradation. SMC is used for water tanks, utility boxes, and architectural panels that require longevity and minimal maintenance.
4. Aerospace and Defense
In the aerospace and defense sectors, SMC is valued for its high strength-to-weight ratio, durability, and resistance to extreme conditions. It’s commonly used for internal components, panels, and casings that demand both strength and weight efficiency.
SMC Manufacturing Process
The manufacturing process of SMC involves a few critical steps:
1. Compounding: The raw materials, including resin, fillers, and fibers, are combined into a uniform sheet.
2. Molding: The sheet is cut and placed into a mold where high pressure and temperature are applied, causing the resin to cure and form the desired shape.
3. Cooling and Finishing: The molded part is cooled and removed from the mold, followed by any necessary trimming or finishing touches.
SMC vs. Other Composites
When compared to materials like Bulk Molding Compound (BMC) or thermoplastics, SMC provides higher structural integrity and is more suitable for larger parts requiring high strength. Unlike BMC, which is used for smaller parts, SMC’s sheet form makes it ideal for applications needing consistent thickness and strength across larger surface areas.
Sustainability and Future Trends in SMC
With growing emphasis on sustainability, SMC manufacturers are increasingly using recycled content and developing resins that reduce environmental impact. The recyclability and lightweight nature of SMC make it a viable material for sustainable production, especially in the automotive industry where weight reduction translates to fuel efficiency and lower emissions.