+8613776545860

SMC stands for Sheet Molding Compound. It is a type of composite material made up of a thermosetting resin, typically polyester, mixed with various reinforcing fibers and fillers. SMC is commonly used in the manufacturing of lightweight, high-strength components for various industries, including automotive, aerospace, electrical, and construction.
The manufacturing process of SMC involves several steps:
1. Preparation of Ingredients:
The resin, reinforcing fibers (such as glass fibers), and fillers (such as calcium carbonate) are mixed together in precise proportions to form the SMC compound.
2. Compression Molding:
The SMC compound is placed into a mold cavity and compressed under high pressure and temperature using hydraulic presses. This compression forces the material to conform to the shape of the mold and ensures uniform distribution of the reinforcing fibers throughout the part.
3. Curing:
The compressed SMC part is heated to cure the thermosetting resin, causing it to harden and permanently bond the reinforcing fibers together. This curing process typically takes place at elevated temperatures for a specific period, depending on the resin system used.
4. Trimming and Finishing:
Once cured, the SMC part is removed from the mold and trimmed to remove any excess material. Additional finishing processes, such as painting, coating, or assembly, may also be performed depending on the desired final product specifications.
SMC offers several advantages over traditional materials like metal or thermoplastics:
1. High Strength-to-Weight Ratio:
SMC components are lightweight yet offer excellent strength and stiffness, making them ideal for applications where weight reduction is critical without compromising structural integrity.
2. Corrosion Resistance:
SMC is inherently resistant to corrosion, making it suitable for use in harsh environments where exposure to moisture, chemicals, or salt is a concern.
3. Design Flexibility:
The molding process allows for complex shapes and intricate designs to be easily produced, enabling manufacturers to create customized components tailored to specific application requirements.
4. Excellent Surface Finish:
SMC parts can be molded with smooth surfaces and high-quality finishes directly from the mold, reducing the need for additional finishing operations and enhancing aesthetics.
5. Electrical Insulation Properties:
SMC is an excellent insulator of electricity, making it suitable for electrical and electronic applications where dielectric properties are required.
Overall, SMC is a versatile and cost-effective material choice for a wide range of applications, offering durability, lightweight construction, and design flexibility.
Application Examples
1.Car Exterior Parts
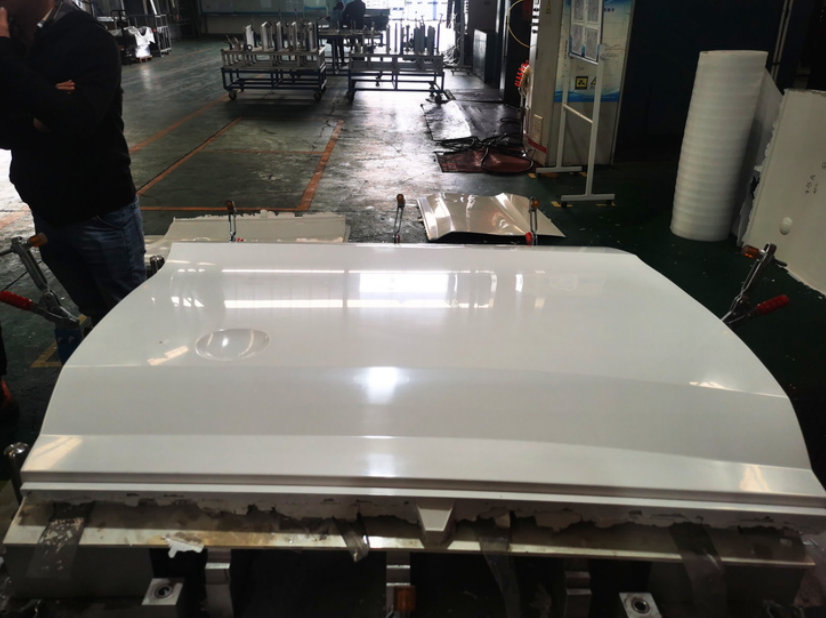
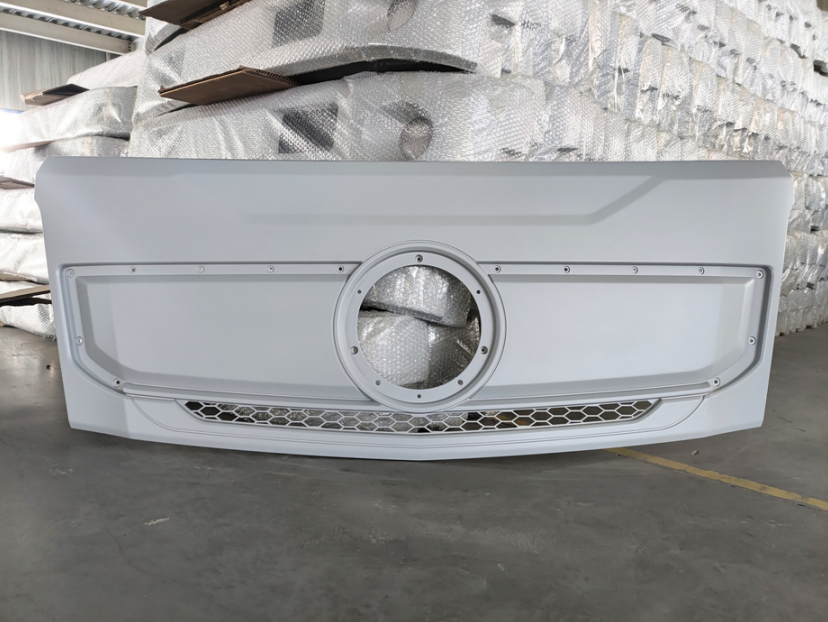
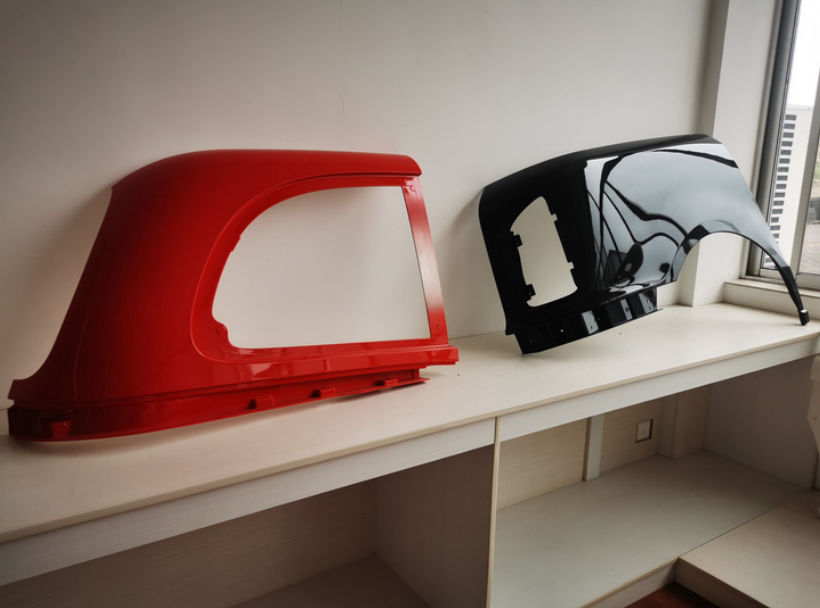
2.Agricultural Vehicles
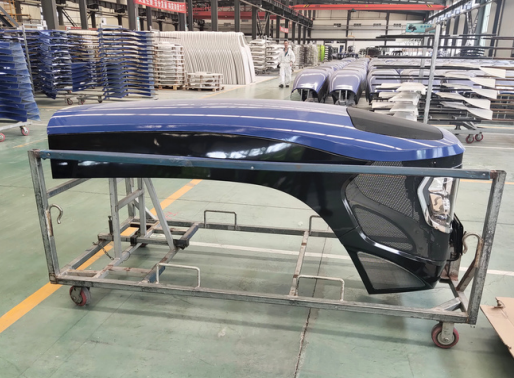
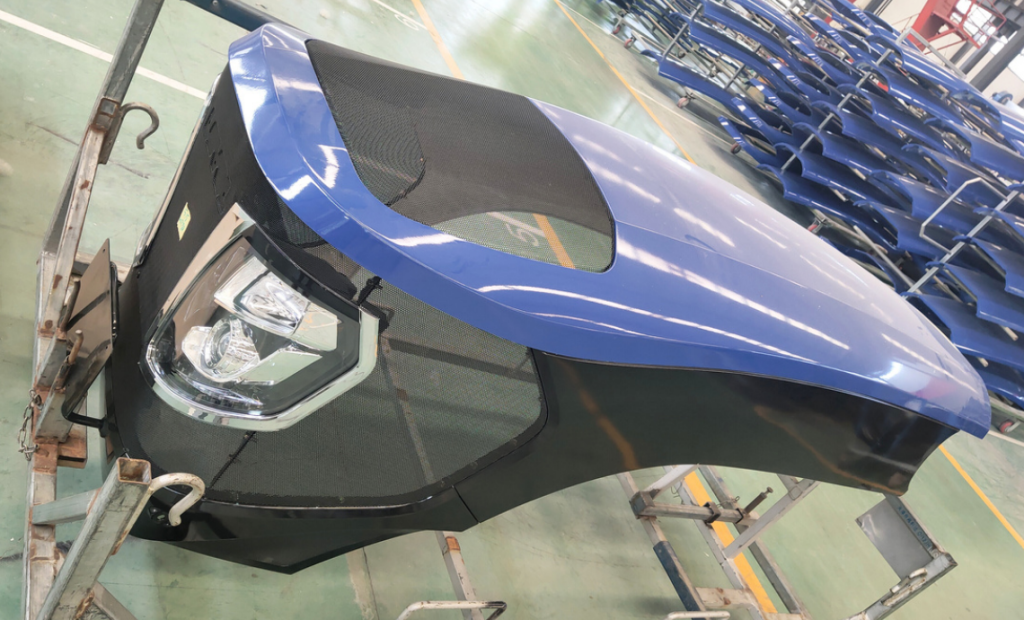
3.Heavy Truck Accessories
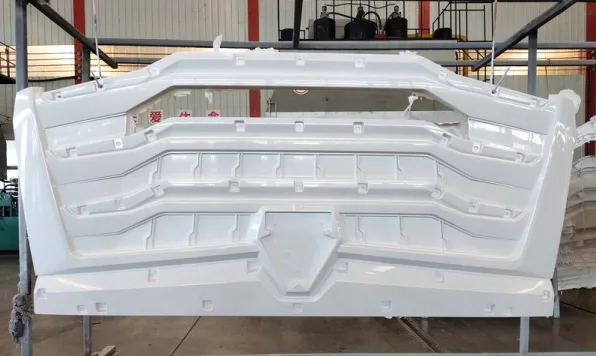
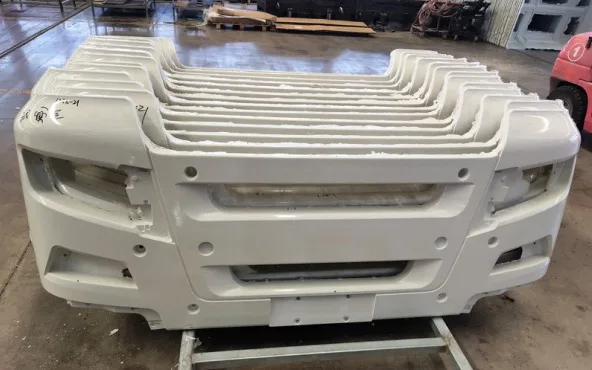
4.Door Panel/Door Skin
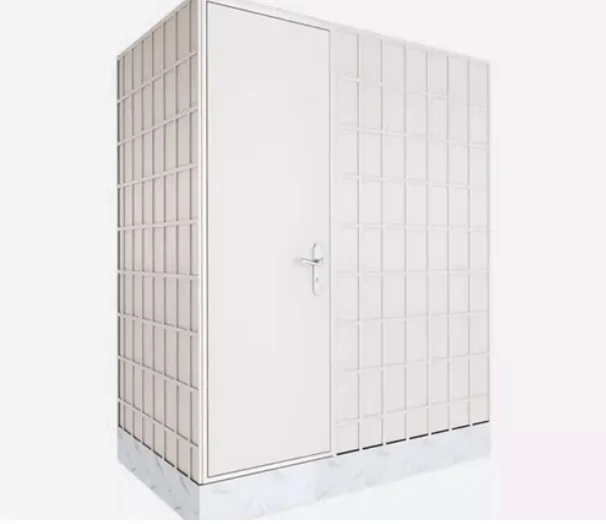
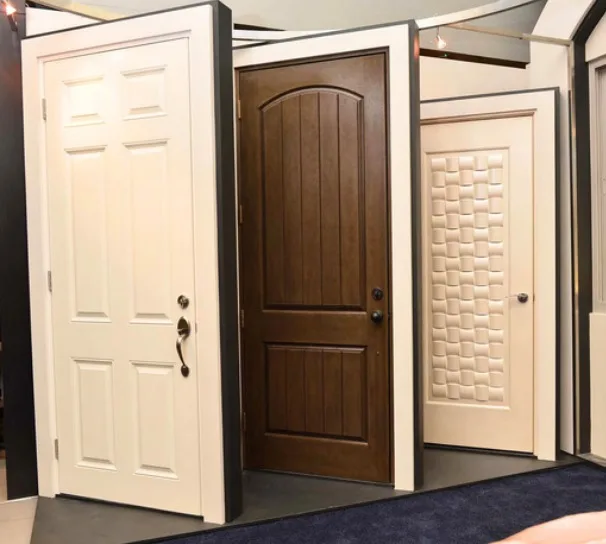
5.and more…