+8613776545860
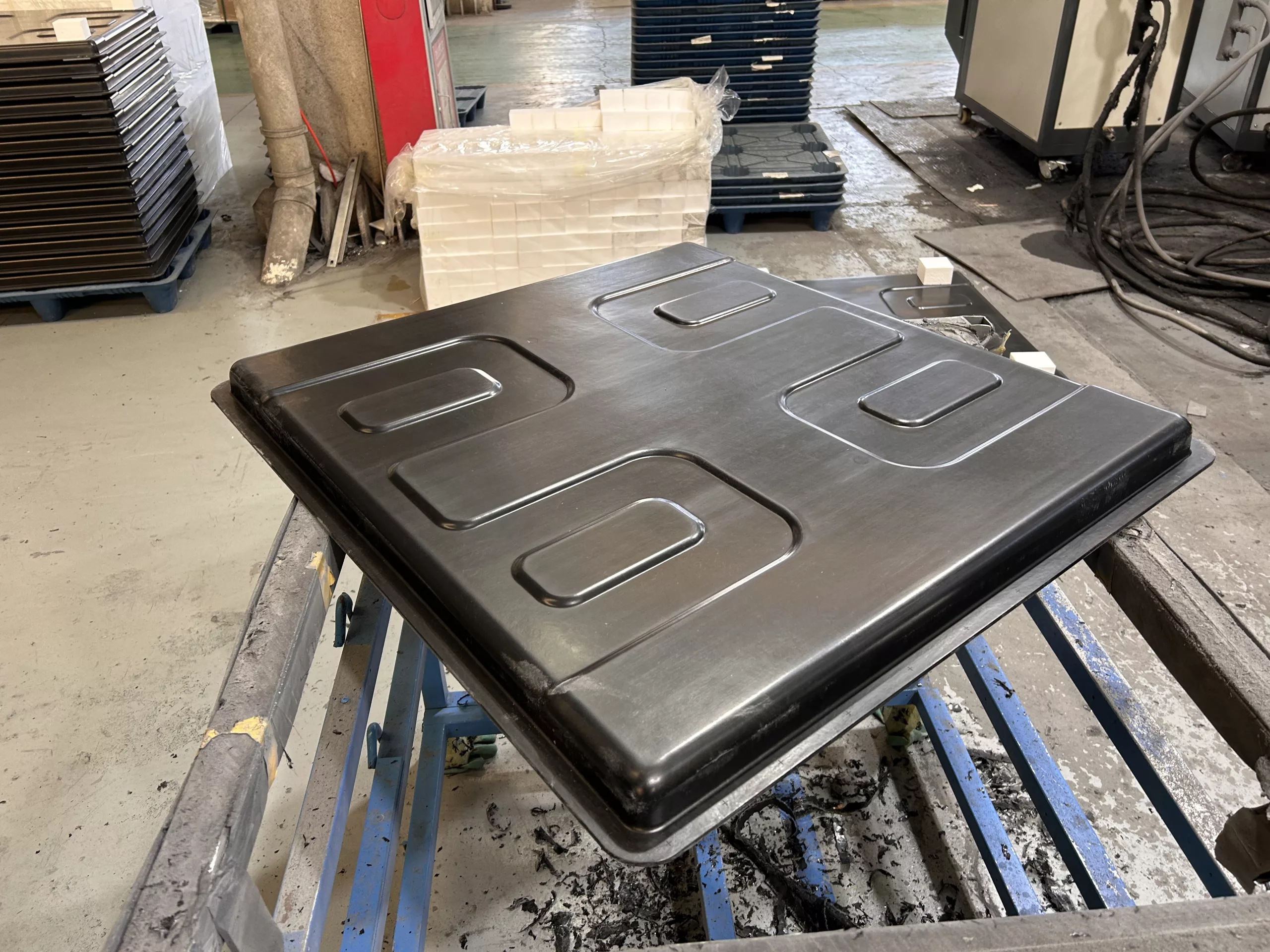
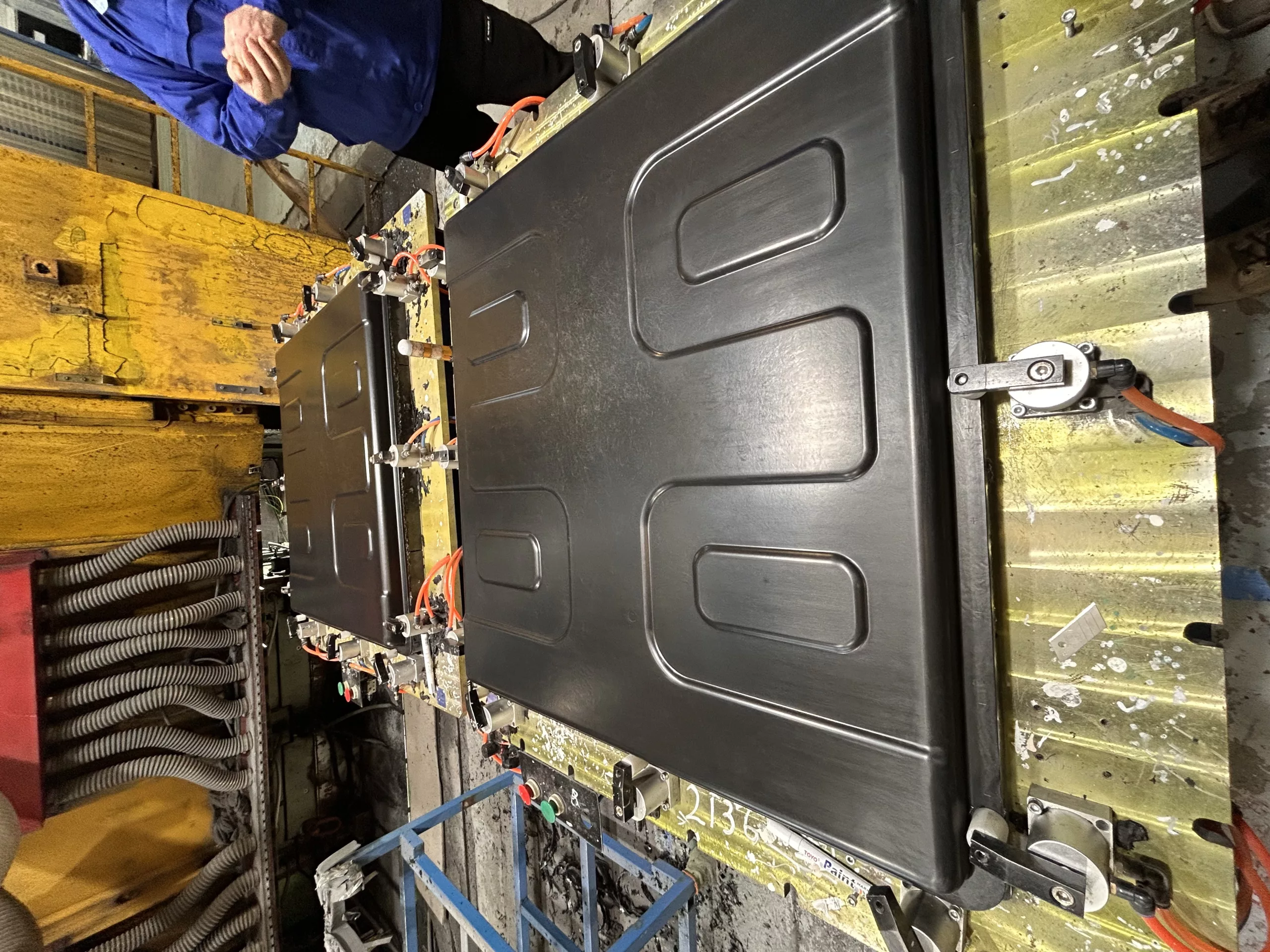
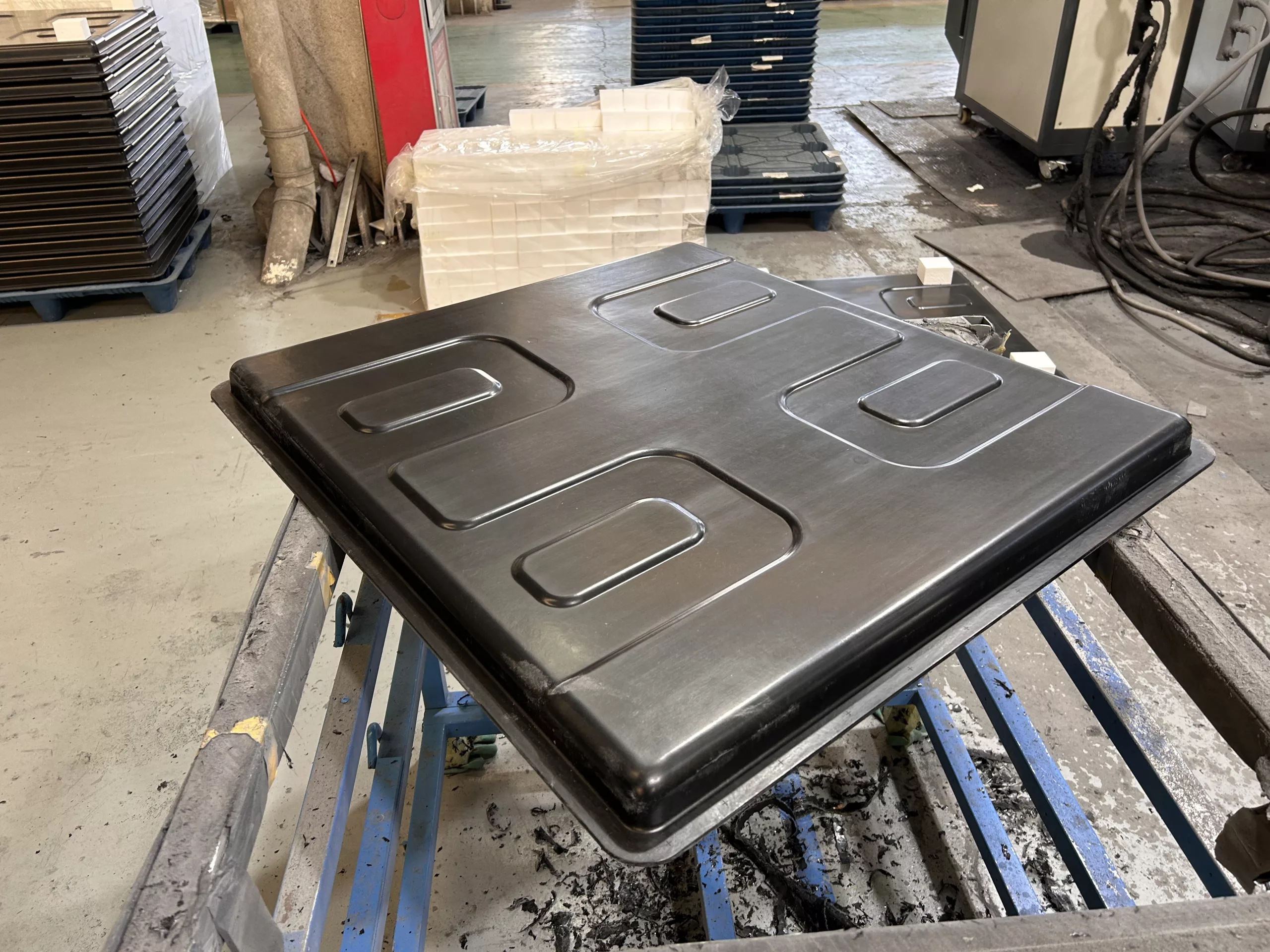
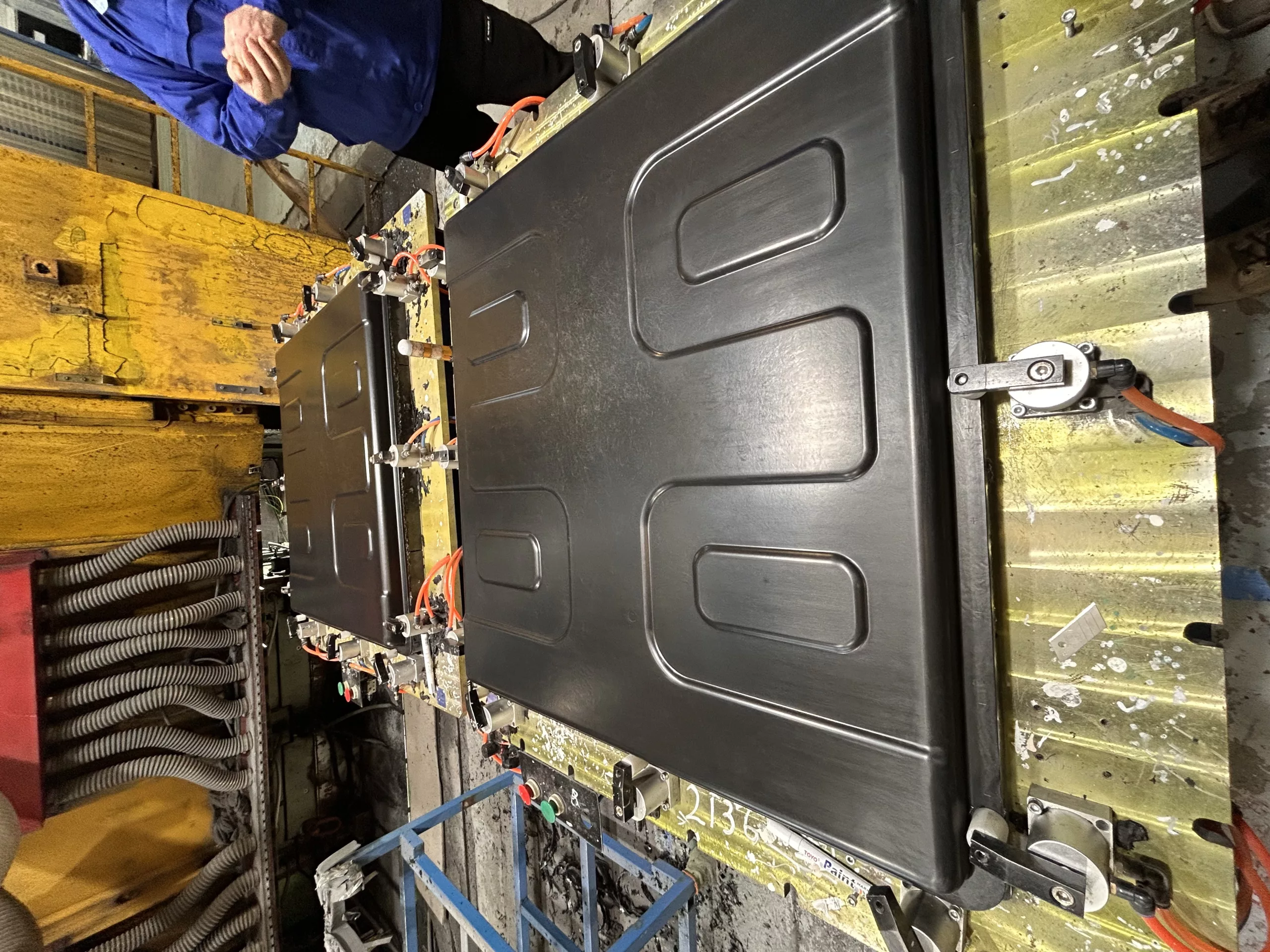
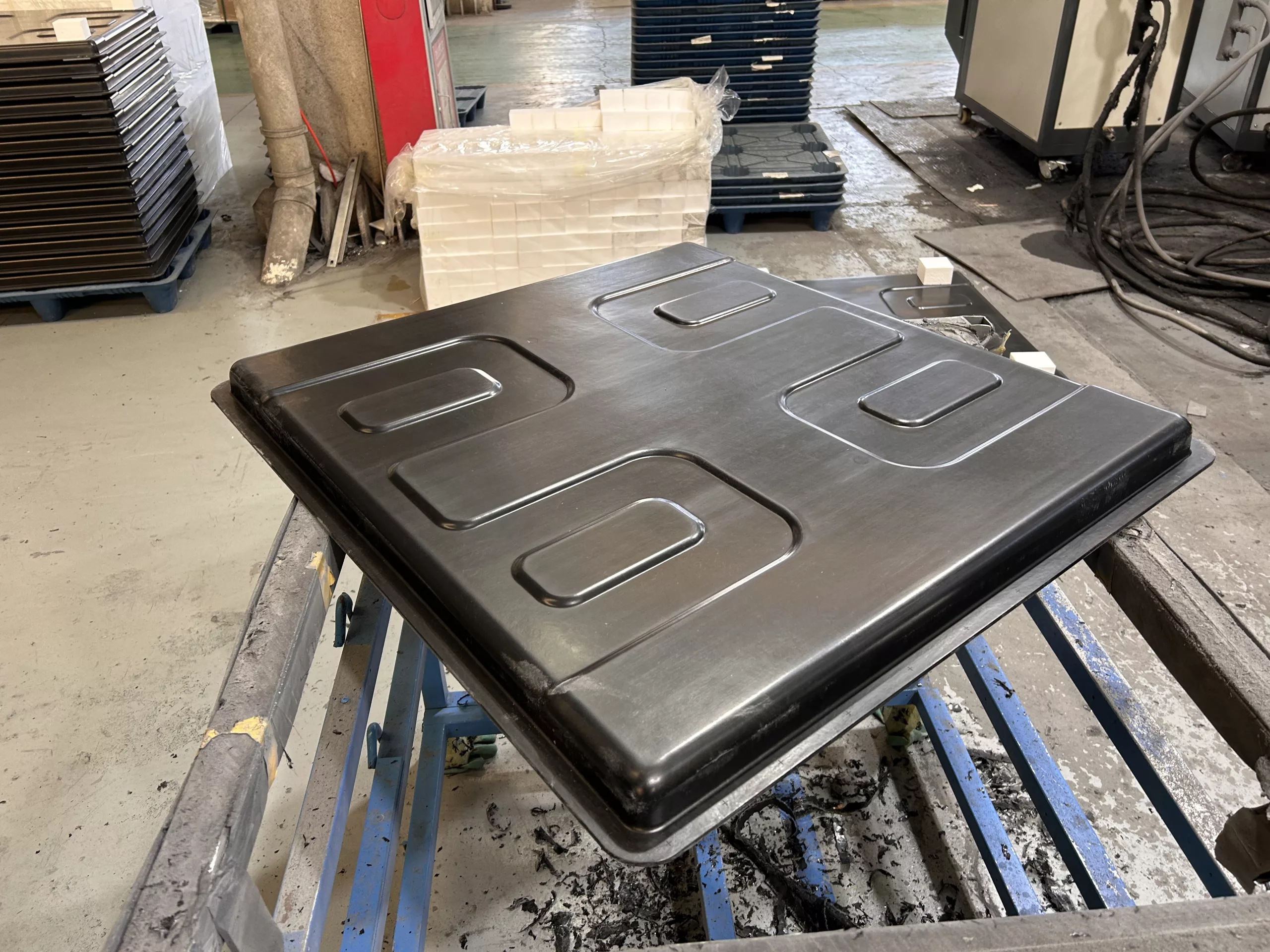
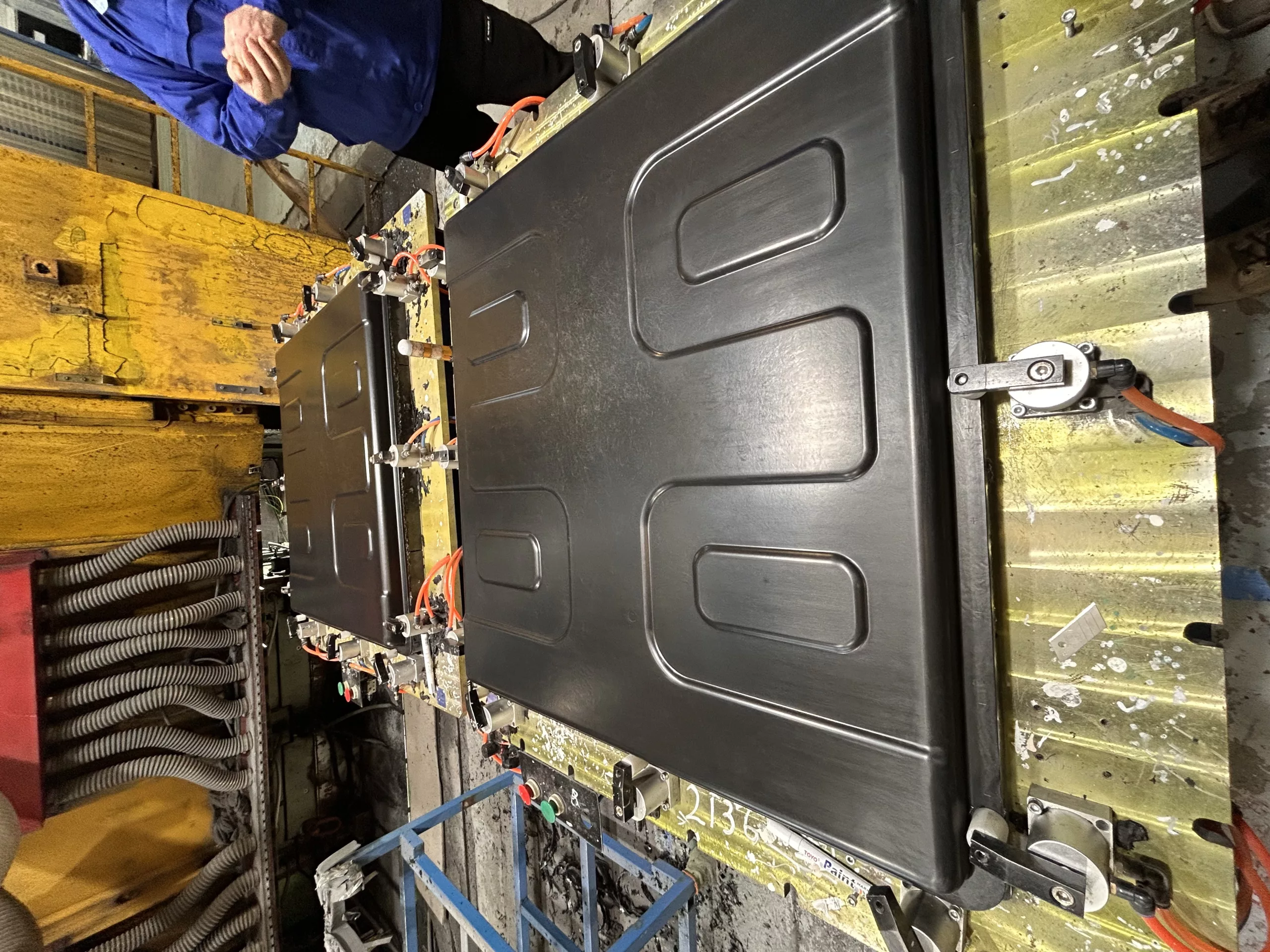
The Role of SMC Sheets in EV Battery Box Cover Manufacturing: A Game-Changer for Electric Vehicles
As electric vehicles (EVs) continue to redefine the automotive industry, manufacturers are under pressure to innovate components that are lightweight, durable, and cost-effective. One critical element in this evolution is the EV battery box cover, which protects the heart of any electric vehicle—the battery. Enter SMC (Sheet Molding Compound) sheets, a revolutionary material transforming the way these covers are produced. In this blog, we’ll explore the application of SMC sheets in EV battery box cover manufacturing, their benefits, and why they’re a perfect fit for the future of mobility.
What Are SMC Sheets?
SMC sheets are composite materials made from a blend of thermosetting resin (typically polyester), glass fibers, and fillers, molded under heat and pressure into strong, lightweight sheets. This unique combination delivers exceptional mechanical properties, making SMC an ideal choice for automotive applications, including EV battery box covers.
Why SMC Sheets for EV Battery Box Covers?
The battery box cover in an electric vehicle serves a vital role: safeguarding the battery pack from environmental factors, impacts, and thermal fluctuations while contributing to the vehicle’s overall efficiency. Here’s why SMC sheets have become a go-to solution in this manufacturing process:
1. **Lightweight Strength**
EVs thrive on efficiency, and every kilogram saved boosts range and performance. SMC sheets offer a high strength-to-weight ratio, providing the robustness needed to protect battery packs without adding unnecessary heft. Compared to traditional metals like steel or aluminum, SMC significantly reduces the weight of battery box covers.
2. **Corrosion Resistance**
Unlike metals, SMC sheets are inherently resistant to corrosion, moisture, and chemicals. This is a game-changer for EVs exposed to harsh weather conditions or road salts, ensuring the battery enclosure remains intact and functional over time.
3. **Thermal Insulation**
Battery packs generate heat during operation, and maintaining optimal temperatures is crucial for performance and safety. SMC’s low thermal conductivity helps insulate the battery, reducing the risk of overheating and enhancing the longevity of the system.
4. **Design Flexibility**
The molding process of SMC allows manufacturers to create complex shapes and integrate features like mounting points or sealing grooves directly into the battery box cover. This flexibility reduces assembly time and costs while meeting the precise specifications of EV designs.
5. **Cost-Effective Production**
SMC sheets enable high-volume production through compression molding, a process that’s both efficient and economical. For automakers scaling up EV production, this translates to lower manufacturing costs without compromising quality.
The Manufacturing Process: How SMC Sheets Become Battery Box Covers
The journey from raw SMC sheets to finished EV battery box covers involves a streamlined yet precise process:
– **Material Preparation**: SMC is prepared by combining resin, fiberglass, and additives into a pliable sheet, which is then cut to size based on the cover’s design.
– **Compression Molding**: The SMC sheet is placed into a heated mold, where pressure and temperature cure it into the desired shape. This step ensures uniformity and structural integrity.
– **Finishing**: Once molded, the cover undergoes trimming, surface treatment, and quality checks to meet automotive standards.
– **Assembly**: The final product is ready to be integrated into the EV battery pack, offering a seamless fit and reliable protection.
This process not only delivers high-quality components but also supports the rapid production cycles demanded by the growing EV market.
Benefits for the EV Industry
The adoption of SMC sheets in EV battery box cover manufacturing aligns perfectly with the industry’s goals of sustainability and performance. Beyond their practical advantages, SMC components are recyclable, contributing to a greener production cycle. Additionally, their durability reduces the need for frequent replacements, enhancing the overall lifecycle value of electric vehicles.
The Future of SMC in EV Manufacturing
As EV technology advances, the demand for innovative materials like SMC sheets will only grow. With ongoing research into improving SMC formulations—such as enhancing flame resistance or incorporating recycled fibers—the potential applications in EV manufacturing are expanding. Battery box covers are just the beginning; SMC could soon play a role in other lightweight, high-strength components across the vehicle.
Conclusion
SMC sheets are revolutionizing EV battery box cover manufacturing by offering a blend of strength, lightweight design, and cost efficiency that traditional materials struggle to match. For automakers and consumers alike, this translates to better-performing, longer-lasting electric vehicles. As the EV industry accelerates toward a sustainable future, SMC sheets are proving to be an essential ingredient in driving that progress forward.