+8613776545860
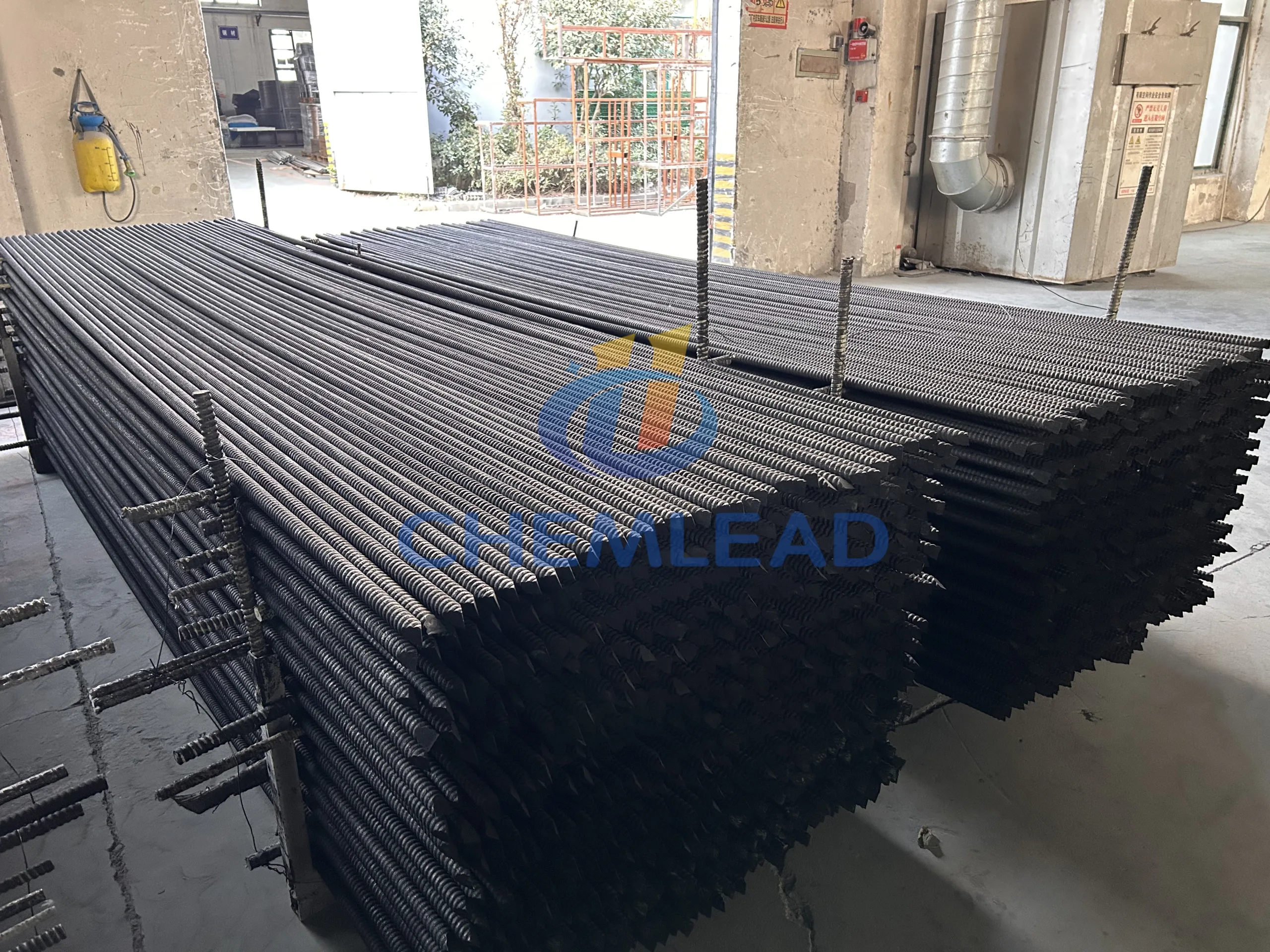
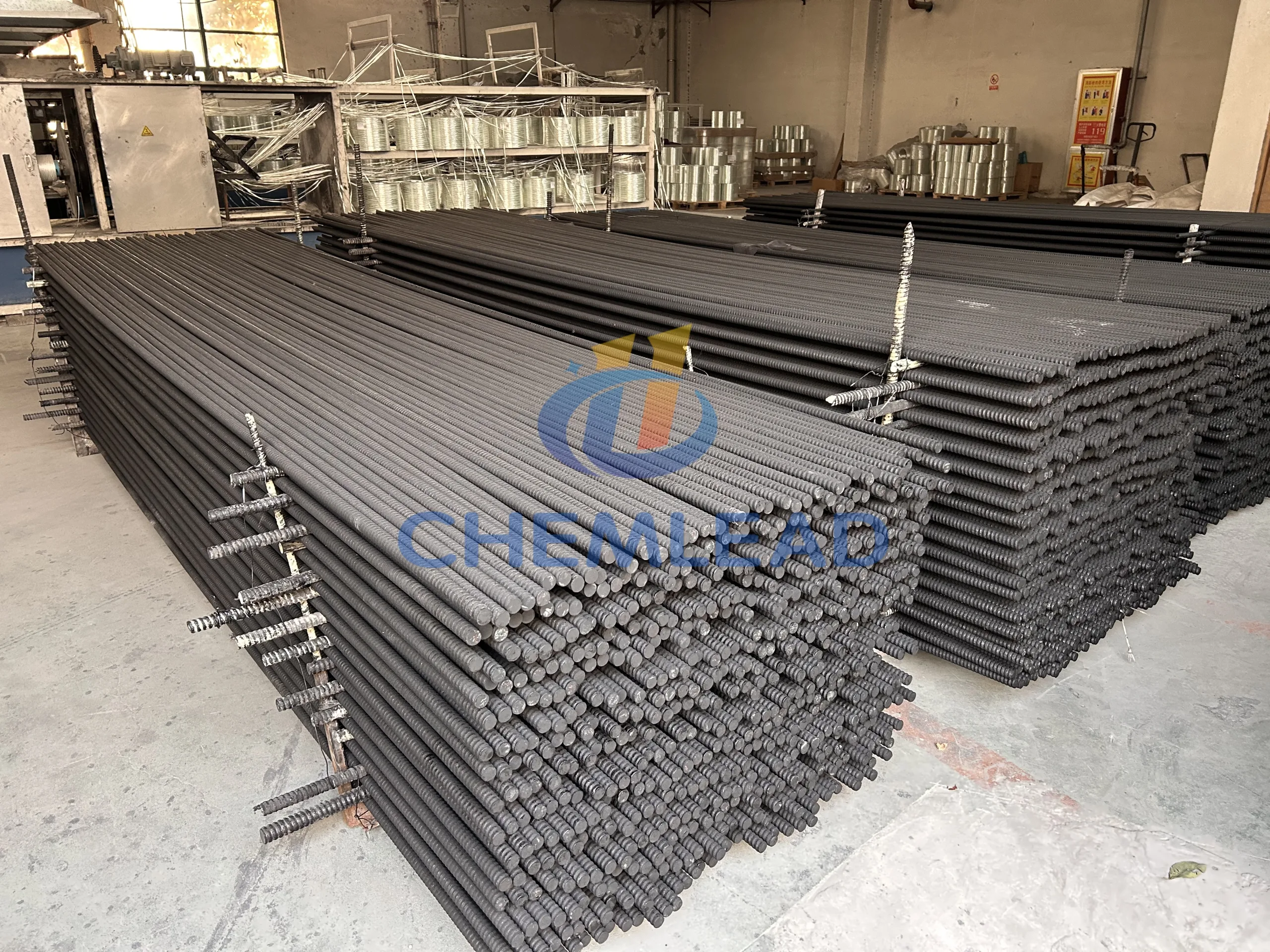
FRP Rockbolts: A Game-Changer for Mining, Tunneling, and Underground Construction
When it comes to ensuring the stability and safety of underground structures such as tunnels, mines, and excavations, rockbolts are an essential component of any ground support system. Traditional rockbolts made of steel have long been the industry standard, but as the need for more durable, lightweight, and corrosion-resistant solutions has grown, FRP (Fiber Reinforced Polymer) rockbolts have emerged as a superior alternative. In this SEO-optimized post, we will explore what FRP rockbolts are, their advantages, applications, and how they are revolutionizing underground construction projects.
What Are FRP Rockbolts?
FRP rockbolts are a modern alternative to traditional steel rockbolts, made from composite materials that combine high-strength fibers (typically glass, carbon, or aramid) with polymer resins. This composite material is designed to provide exceptional strength, durability, and corrosion resistance, making it ideal for underground ground support applications in harsh environments.
FRP rockbolts are lightweight, non-corrosive, and capable of withstanding the extreme conditions commonly found in mining, tunneling, and construction projects. They are designed to be installed in the same way as traditional rockbolts but offer several performance benefits that make them a preferred choice in certain geological conditions.
Key Benefits of FRP Rockbolts
1.Corrosion Resistance:
•One of the most significant advantages of FRP rockbolts is their corrosion resistance. Unlike steel rockbolts, which are vulnerable to rust and degradation in moist or chemically aggressive environments, FRP rockbolts do not corrode. This makes them ideal for use in high-moisture environments, such as in coastal or underground mining operations, where water and chemical exposure can rapidly deteriorate traditional steel bolts.
2.Lightweight and Easy to Handle:
•FRP rockbolts are significantly lighter than their steel counterparts, which makes them easier to transport, handle, and install. This reduces labor costs and the need for heavy equipment, improving overall efficiency on site. The lightweight nature also reduces the load on the surrounding rock structure, making them an excellent choice for projects with weight limitations.
3.High Strength-to-Weight Ratio:
•Despite being lightweight, FRP rockbolts have an impressive strength-to-weight ratio. The fibers used in FRP composites, such as glass or carbon, provide exceptional tensile strength, allowing FRP rockbolts to perform under high-stress conditions. This makes them suitable for a variety of underground applications where stability and load-bearing capacity are critical.
4.Non-Magnetic Properties:
•FRP rockbolts are non-magnetic, which is particularly important in environments where magnetic interference can cause issues, such as in certain mining operations or around sensitive equipment. This non-magnetic property makes them ideal for use in environments where electronic devices and machinery are in operation.
5.Durability and Long Service Life:
•The inherent properties of FRP materials contribute to a longer service life for rockbolts. They are resistant to a wide range of chemicals and environmental factors such as UV radiation, extreme temperatures, and mechanical wear. This makes them more durable and reduces the need for frequent maintenance or replacement, ultimately lowering project costs over time.
6.Environmental Benefits:
•FRP materials are generally more eco-friendly than traditional steel. Many FRP rockbolts are made using recyclable materials and manufacturing processes that produce less environmental impact. Additionally, the longer lifespan of FRP rockbolts means fewer replacements are necessary, further reducing waste.
Applications of FRP Rockbolts
1.Mining Operations:
•In mining, where ground stability is crucial to worker safety, FRP rockbolts are increasingly being used to secure rock masses and support tunnels. Their high strength and corrosion resistance make them ideal for deep mining environments, where harsh conditions can quickly deteriorate steel bolts.
2.Tunneling Projects:
•FRP rockbolts are commonly used in tunnel construction, particularly in high-moisture environments like subway systems, drainage tunnels, and water diversion tunnels. Their lightweight and durable nature make them an excellent choice for ensuring the structural integrity of tunnels over long periods.
3.Underground Civil Engineering:
•Whether it’s for underground parking garages, infrastructure development, or the construction of underground facilities, FRP rockbolts provide reliable support in environments where steel bolts might fail due to corrosion. They are used in both temporary and permanent ground support systems to stabilize soil and rock.
4.Slope Stabilization:
•FRP rockbolts can be used in civil engineering applications such as slope stabilization and rockfall protection. Their high tensile strength helps secure unstable rock or soil layers, reducing the risk of landslides and rockfalls in mountainous or hilly regions.
5.Dam Construction:
•In the construction of dams and related hydraulic structures, FRP rockbolts are used to stabilize rock surfaces and improve the integrity of the surrounding environment, ensuring the long-term durability of these critical infrastructures.
How to Choose the Right FRP Rockbolt for Your Project
Selecting the right FRP rockbolt for a specific project requires understanding the unique geological and environmental conditions of the site. Here are some key factors to consider when choosing FRP rockbolts:
1.Geological Conditions: The type of rock or soil, its strength, and the presence of moisture or chemicals will determine the ideal material and strength for the rockbolt. For soft, unstable rocks, higher strength and longer rockbolts may be necessary.
2.Environmental Factors: If your project is located in an area with high humidity, chemical exposure, or extreme temperatures, FRP rockbolts are likely to be the best option due to their corrosion resistance and durability.
3.Installation Method: Depending on the application, FRP rockbolts can be installed using conventional drilling equipment. However, for certain applications like self-drilling rockbolts, ensure the FRP bolts are compatible with the drilling equipment and installation methods you plan to use.
4.Load-Bearing Capacity: The load requirements of your project will influence the type of FRP rockbolt you need. Higher-strength bolts or multi-strand cable bolts may be necessary for high-stress areas like deep mines or large tunnels.
Conclusion
FRP rockbolts are transforming underground construction and mining projects by offering a combination of strength, corrosion resistance, and durability that traditional steel rockbolts simply cannot match. Whether you’re working in mining, tunneling, or civil engineering, FRP rockbolts provide a superior solution for ground stabilization and structural support. With their lightweight design, excellent performance in harsh environments, and environmental benefits, FRP rockbolts are quickly becoming the go-to choice for engineers and contractors looking to improve safety and efficiency in underground projects.
If you’re looking to integrate FRP rockbolts into your next project, make sure to consult with experts who can help you select the best solution tailored to your specific needs. The future of underground support is here, and it’s FRP.